All About Alcast Company
Table of Contents5 Easy Facts About Alcast Company ExplainedGetting My Alcast Company To WorkThe Main Principles Of Alcast Company The Basic Principles Of Alcast Company The smart Trick of Alcast Company That Nobody is Talking AboutAlcast Company Can Be Fun For Anyone
The subtle distinction depends on the chemical material. Chemical Contrast of Cast Aluminum Alloys Silicon promotes castability by decreasing the alloy's melting temperature level and improving fluidity during casting. It plays a crucial function in permitting detailed molds to be filled accurately. Furthermore, silicon adds to the alloy's strength and wear resistance, making it important in applications where durability is critical, such as automotive components and engine components.It likewise enhances the machinability of the alloy, making it much easier to refine into finished products. In this way, iron adds to the overall workability of aluminum alloys. Copper raises electric conductivity, making it advantageous in electrical applications. It also enhances corrosion resistance and adds to the alloy's overall toughness.
Manganese adds to the stamina of aluminum alloys and improves workability (Aluminum Castings). It is generally utilized in wrought aluminum items like sheets, extrusions, and accounts. The visibility of manganese help in the alloy's formability and resistance to fracturing throughout manufacture procedures. Magnesium is a light-weight element that provides strength and influence resistance to light weight aluminum alloys.
The 7-Second Trick For Alcast Company
It permits the manufacturing of light-weight elements with superb mechanical properties. Zinc improves the castability of aluminum alloys and aids regulate the solidification procedure throughout spreading. It improves the alloy's stamina and hardness. It is typically found in applications where detailed forms and great details are required, such as ornamental castings and particular vehicle components.
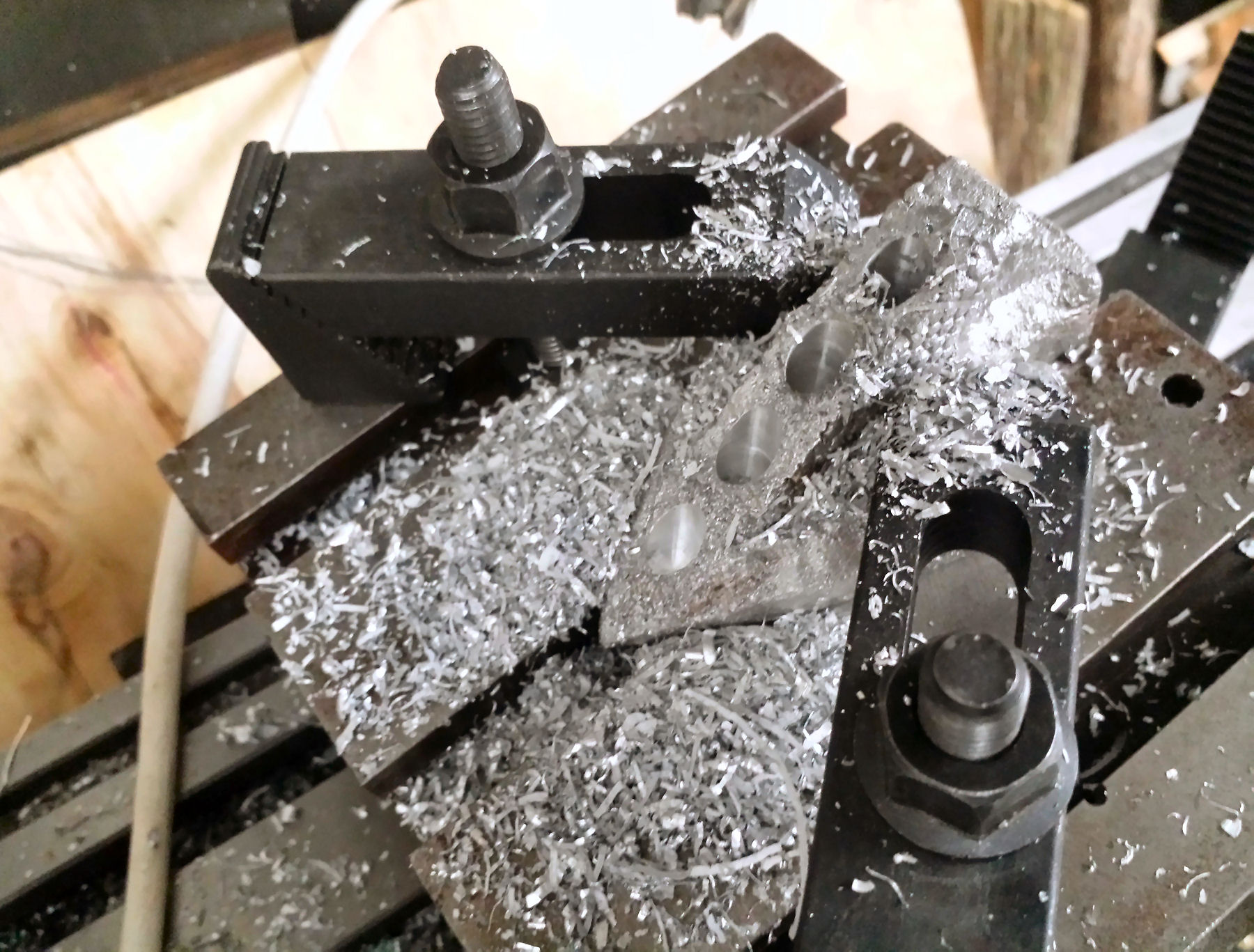
The primary thermal conductivity, tensile strength, yield stamina, and prolongation vary. Select ideal resources according to the efficiency of the target item generated. Amongst the above alloys, A356 has the highest thermal conductivity, and A380 and ADC12 have the most affordable. The tensile restriction is the contrary. A360 has the most effective return toughness and the highest possible prolongation price.
Alcast Company Can Be Fun For Anyone

In precision spreading, 6063 is well-suited for applications where complex geometries and top notch surface coatings are critical. Instances include telecommunication rooms, where the alloy's exceptional formability enables for sleek and cosmetically pleasing layouts while preserving architectural honesty. In a similar way, in the Illumination Solutions industry, precision-cast 6063 elements develop classy and reliable lighting fixtures that require intricate forms and excellent thermal performance.
The A360 shows premium prolongation, making it excellent for facility and thin-walled elements. In precision spreading applications, A360 is fit for markets such as Consumer Electronics, Telecommunication, and Power Devices.
The Ultimate Guide To Alcast Company
Its unique residential or commercial properties make A360 a beneficial choice for accuracy casting in these markets, boosting product durability and top quality. Aluminum alloy 380, or A380, is an extensively utilized casting alloy with numerous distinctive attributes. It provides superb castability, making it a suitable choice for accuracy casting. A380 exhibits excellent fluidity when molten, making certain intricate and detailed molds are properly replicated.
In precision casting, light weight aluminum 413 beams in the Customer Electronics and Power Tools sectors. This alloy's exceptional rust resistance makes it an outstanding option for outside applications, guaranteeing durable, long lasting products in the stated markets.
Little Known Questions About Alcast Company.
The aluminum alloy you select will considerably influence both the spreading process and the homes of the last product. Because of this, you need to make your choice carefully and take an informed method.
Figuring out the most ideal aluminum alloy for your application will certainly imply considering a vast variety of qualities. The first group addresses alloy features that affect the production process.
Alcast Company - Truths
The alloy you pick for die casting directly influences a number of aspects of the spreading process, like exactly how simple the alloy is to collaborate with and if it is prone to casting issues. Warm breaking, additionally referred to as solidification splitting, is a common die spreading defect for light weight aluminum alloys that can cause interior or surface-level splits or splits.
Specific light weight aluminum alloys are Recommended Site more vulnerable to warm cracking than others, and your choice needs to consider this. Another typical defect discovered in the die spreading of aluminum is die soldering, which is when the actors stays with the die walls and makes ejection tough. It can harm both the actors and the die, so you ought to try to find alloys with high anti-soldering homes.
Corrosion resistance, which is currently a noteworthy characteristic of light weight aluminum, can differ significantly from alloy to alloy and is an important characteristic to think about depending on the ecological conditions your product will be exposed to (Aluminum Casting). Use resistance is an additional residential property generally sought in light weight aluminum items and can differentiate some alloys